Lean engineering practices work to improve the efficiency and efficacy of engineering departments within manufacturing organizations.
Lean engineering can help organizations become more innovative and competitive, while saving money and optimizing resource efficiency. This article will cover some of the essential principles and practices of Lean engineering.
AgilePlace Free Trial: AgilePlace Online Kanban Software
Sign up for a 30-day free trial and you and your team can start building online Kanban boards today. Experience for yourself how AgilePlace supports continuous delivery initiatives, eliminates waste and improves your team’s delivery processes and speed.
Börja utvärdera kostnadsfritt • AgilePlace Free TrialLean Portfolio Management for the Enterprise: What Is It and How Is It Changing Value Delivery?
Läs vitbok • Hantering av företagets produktutbud med Lean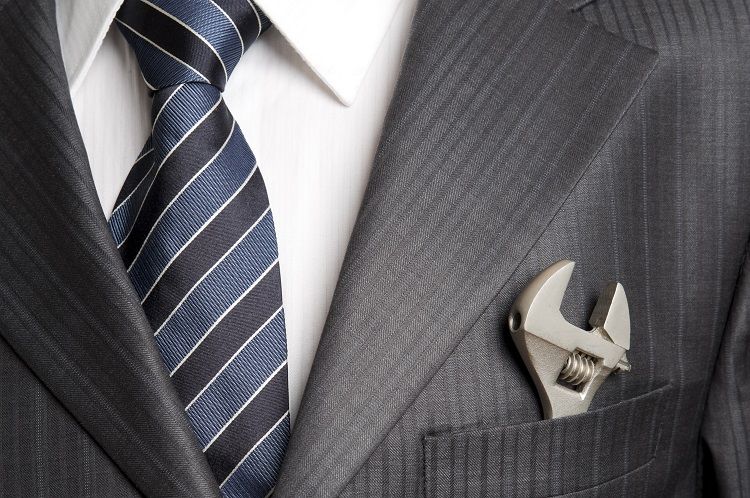
What is Lean Engineering?
Lean engineering is a holistic approach to engineering that influences:
- Leadership principles and practices within engineering organizations
- Team structures
- Team processes and process visualization
- Tools and technologies used to optimize for efficiency
- Management and creation of engineering intelligence
Lean engineering practices aim to eliminate waste while creating more value for the customer.
Defining Waste
In manufacturing, where products move from one step to the next until they are completed, it’s easy to see where waste is created: You just have to look for physical evidence of bottlenecks, blockers, etc.
But what is waste in engineering, where the majority of the “product” is inside the minds of employees? Waste, in Lean engineering, is defined as anything activity, process, or product that does not add value to the customer. There are many sources of waste in engineering, including:
- Overproduction: Generating reports, tests, and other unneeded analyses
- Inventory: Unfinished analyses, reports, and tests
- Transportation: Handoffs, complex validations of decisions and processes
- Unnecessary movement
- Waiting: For decisions, input, or feedback
- Defects: Rework due to wrong requirements or inputs; errors in trying to correct the problem
- Overprocessing: Unnecessary activities, tasks, and processes, especially for analysis and communication; “reinventing the wheel” with each new task
- Unused employee potential: Not engaging engineers in process improvements for engineering
Applying Lean concepts to engineering can help reduce uncertainty, boost productivity, and provide a systematic method for process improvement.
Key Lean Engineering Concepts
Cellular manufacturing
The cellular manufacturing approach is often used by Lean engineering organizations. The goal of cellular manufacturing is to help teams work as quickly and efficiently as possible, helping to reduce cycle time and inventory to meet market response times.
Cellular manufacturing uses “cells” composed of one or multiple different machines which accomplish a specific task. Products move from one cell to the next, moving through the manufacturing process.
Arranging machines, or workstations, this way allows for maximum flexibility. Because the machines are mostly automatic, engineering changes, from minor tweaks to entire design overhauls, can be done relatively quickly and easily.
Takt time
Takt time is a measure of the rate of production needed to meet demand for a product. It is the average time between the start of production of one unit and the start of production of the next unit, set to match the rate of customer demand. If a process or manufacturing line is unable to produce at takt time, Lean engineering organizations use demand leveling, additional resources, or process re-engineering to resolve the issue.
Standardized work
Implementing a system of standardized work allows Lean engineering organizations to improve efficiency, communicate more effectively, and share learnings across the organization. Methods, materials, tools, processes, and tasks can all be standardized to create room to innovation and efficiency in the organization.
Continuous flow (limiting WIP)
In order to achieve continuous flow, Lean engineering organizations rely on a Lean concept called limiting WIP, or work-in-process. Work-in-process is any piece of work actively being worked on.
Excess WIP is the killer of productivity, because when a team has too much work in progress, the time, energy, and effort is divided across multiple pieces of work, making it harder to bring any one thing across the finish line.
Continuous flow encourages Lean engineering organizations to stop starting and start finishing work, whether that means knowledge work, or products on an assembly line.
Pull system
Related to the concept of continuous flow is a pull system. Usually visualized through the use of a Kanban board, a pull system is one in which work is “pulled” into “doing” as capacity allows, by the people doing the work. Usually, work enters the system due to a customer request – for example, by ordering a product.
Using a pull system encourages teams to actively prioritize and complete work as it is actually needed. This is the opposite of a push system, in which a team begins work without regard to existing WIP, inevitably causing a WIP overload that slows down the productivity of the team or organization.
The 5 Whys
The 5 Whys is a Lean engineering method of root cause analysis, that encourages exploratory thought and data-driven problem-solving. The concept is simple: You begin with a problem statement, then ask “Why?”, answering until the answers became reductionist or absurd. For example:
Problem statement: Our QA process creates a bottleneck in our system, slowing down progress up and downstream.
Why?
Because our QA cycle time is slow.
Why?
Because we only have 3 people doing QA, but 15 people creating work that needs to be tested.
Why?
Because when we combined three engineering teams, only one of them had dedicated resources to QA.
Why?
Because…. We didn’t think we needed it?
In this example, it seems like the team needs to dedicate more people to QA, in order to keep progress moving and eliminate the bottleneck in the process. It’s worth noting that the “5” part of the 5 Whys is merely a suggestion; you might find your root cause in 3 or 7 whys.
Lean engineering organizations use the 5 Whys to identify root causes of anything getting in the way of efficiency, flow, and speed.
PDCA
The PDCA cycle is a logical method for solving problems. You can think of it as the next step to problem solving after conducting the 5 Whys. PDCA stands for:
Plan: Create a plan to achieve a goal. Include success criteria and anticipated results.
Do: Implement the plan.
Check: Measure and analyze the results. Compare them to your anticipated and reflect on discrepancies between the two.
Act: Implement necessary adjustments to achieve intended goal.
The PDCA cycle is a helpful way for Lean engineering organizations to practice the Lean concept of continuous improvement.