Inhalt
Every business runs on various processes, or a set of activities to accomplish an objective. These processes help maintain order and consistency and should also increase efficiency. However, processes often become unwieldy over time. When that happens, they end up creating delays and eating up costs. As a result, you need to go through process improvement exercises on a regular basis.
19 Process Improvement Ideas to Add to Your Toolkit
Identify problems, brainstorm solutions, and implement meaningful changes to your process.
E-Book lesen • 19 Process Improvement Ideas to Add to Your ToolkitErste Schritte mit Lean
Lean ist eine Denkweise, die Ihnen hilft, intelligentere Entscheidungen darüber zu treffen, wie Sie Ihre Zeit, Energie und Ihr Geld investieren können.
E-Book lesen • Erste Schritte mit Lean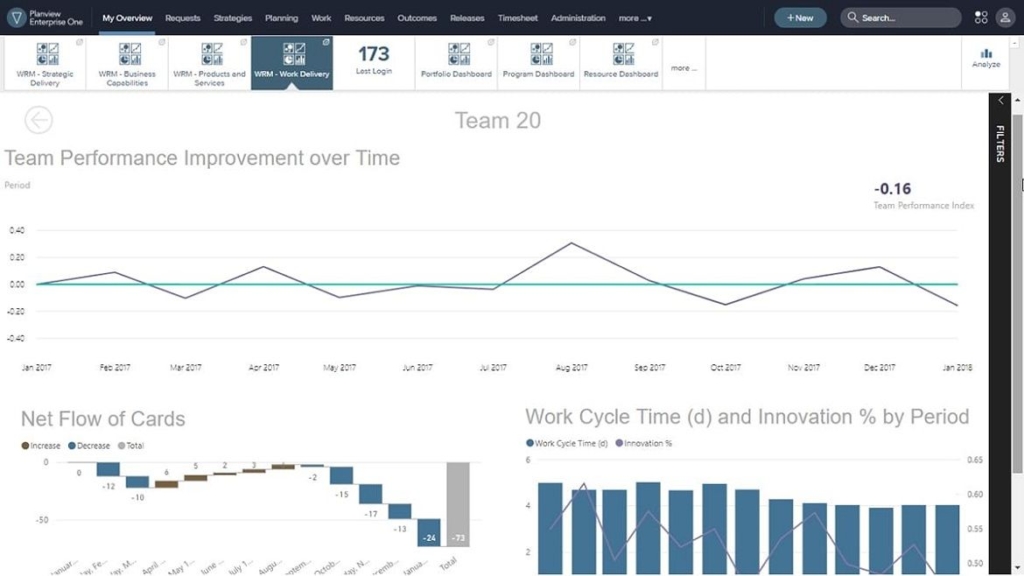
Process improvement is exactly what it sounds like: An effort to make core business processes better so that you improve the output of your work. Ideally, process improvement should lead to more effective workflows as well as more efficient ones.
How do you go about improving your processes? Here are four process improvement examples to get you started.
Examples of Process Improvement Projects
There are numerous ways you can improve your processes, so where should you start? These four process improvement examples typically lead to the most immediate impact:
Vermeiden Sie Verschwendung
One of the best examples of process improvement projects centers around waste. Specifically, if you can identify and eliminate areas of waste within your processes, you can save time and produce higher quality end results.
One of the best ways to eliminate waste is to rely on Lean principles. Lean calls for teams to look for eight kinds of waste:
- Defekt
- Excess processing
- Überproduktion
- Non-utilized talent
- Sitting inventory
- Products waiting for the next step
- Unnecessary moving of products
- Inefficient motion of people
If you can identify any of these types of waste and restructure your processes to eliminate them, you’ll be well on your way toward more efficient processes that deliver value faster.
Reduce costs
Reducing costs is one of the process improvement examples that focuses more on overall effectiveness than efficiency. That said, reducing costs can also help eliminate waste and therefore increase efficiency.
- Look for waste in the form of duplicate or unnecessary tasks
- Identify opportunities to better allocate resources or automate manual tasks
- Review the order of tasks within processes, and even evaluate materials used
While reducing costs is an easy way to improve your processes, this is one of the examples of process improvement projects with which you must be careful, since you don’t want to reduce costs at the expense of quality.
Improve communication and collaboration
The next of our process improvement examples is all about improving communication and collaboration. Unlike the previous two examples, this approach centers entirely around your people. Nevertheless, achieving this improvement often necessitates help from software.
Improving communication and collaboration requires you to eliminate boundaries so that team members can easily share (and find) feedback and ideas on a regular basis. Ideally, this improvement should help people communicate clearly and fully the first time around to reduce the amount of back and forth communications.
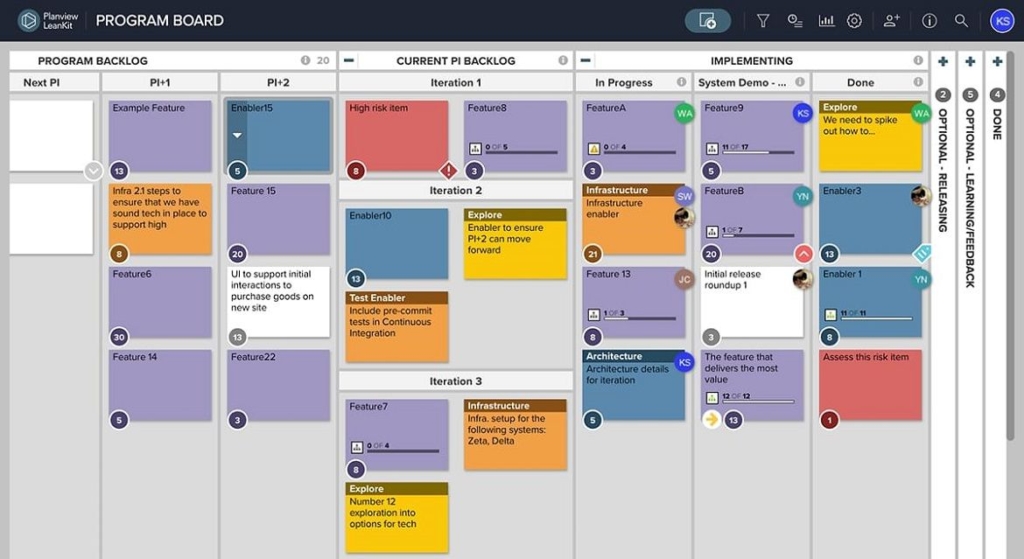
Software can help improve communication and collaboration by connecting people more closely (even when they work in two entirely different locations) and by putting all relevant communications in a single place. Ultimately, it should lead to fewer emails, which means workers can spend less time digging through their inboxes trying to find answers and more time getting work done.
Enhance process visualization
The last of our process improvement examples comes down to understanding the various processes you have in place. This understanding is important for taking on any process improvement efforts in the first place.
All the examples of process improvement projects listed here require a deep understanding of your processes, including:
- The various steps involved
- The time it takes to complete each step and the overall process
- Who typically works on each step
The only way to achieve this understanding is through process visualization, or the ability to view and diagram each step of the process.
If you can enhance your process visualization capabilities, for example by using a project management approach like Kanban, you can more easily identify issues like bottlenecks and the root causes of those issues. In turn, this visualization will make it easier to resolve issues and improve your processes.
Process Improvement Goal Examples
Taking on any of these examples of process improvement projects is great, but what happens next? Ideally, you should achieve one or more of these process improvement goal examples:
- Better quality products: One of the top process improvement goals is to deliver better quality products to your customers. The examples of process improvement projects outlined here can help achieve this goal by better connecting team members to facilitate idea sharing and by improving resource allocation to make sure you fully utilize everyone’s skills.
- Improved service offerings: Making process improvements should also help deliver better service around your products by helping those in service roles access answers to customer questions faster and by ensuring they have the right information to answer those questions fully and correctly the first time around.
- Faster delivery cycles: By eliminating waste and improving communication and collaboration, process improvement projects should lead to faster delivery cycles. Achieving faster delivery cycles is one of the most important process improvement goals in today’s fast-paced, highly competitive markets in which companies must deliver more value to customers faster.
- Faster billing cycles: Faster billing cycles are an important part of faster delivery cycles, as billing needs to keep up with the pace of delivery to ensure that all the parts, software, and workers needed throughout the process are ready to go at all times. This process improvement goal is important to keeping cash flowing through the business.
- Increased efficiency in production: The last of our process improvement goals examples is increased efficiency, which covers more than faster delivery cycles. While increased efficiency in production can absolutely improve the speed of delivery cycles, it can also lead to a smarter (and less wasteful) use of resources, allowing your business to accomplish more in the same amount of time and/or with the same amount of resources.
Remember: Process Improvement Isn’t a One-and-Done Exercise
Now that you have the top four examples of process improvement projects and the goals those projects can help you achieve, you’re ready to go out and put these process improvement examples into action.
Before you do, remember one last point: These process improvement examples aren’t one-and-done exercises. You should approach all these examples of process improvement projects as ongoing efforts, since you want to continuously improve what you’re doing.
Opportunities for continuous improvement when it comes to process improvement examples like those outlined here include:
- Collecting feedback and ideas from the teams closest to the projects
- Conducting regular training for workers
- Running time audits to identify waste and set ideal standards
With that said, you now have everything you need to put these process improvement examples into action on an ongoing basis to achieve your top goals.