BMW Group
BMW Group Expands into New Markets by Using Value Stream Management to Improve Agility, Efficiency, and Quality
Learn how BMW Group found success using Value Stream Management and watch an on-demand demo of the solution.
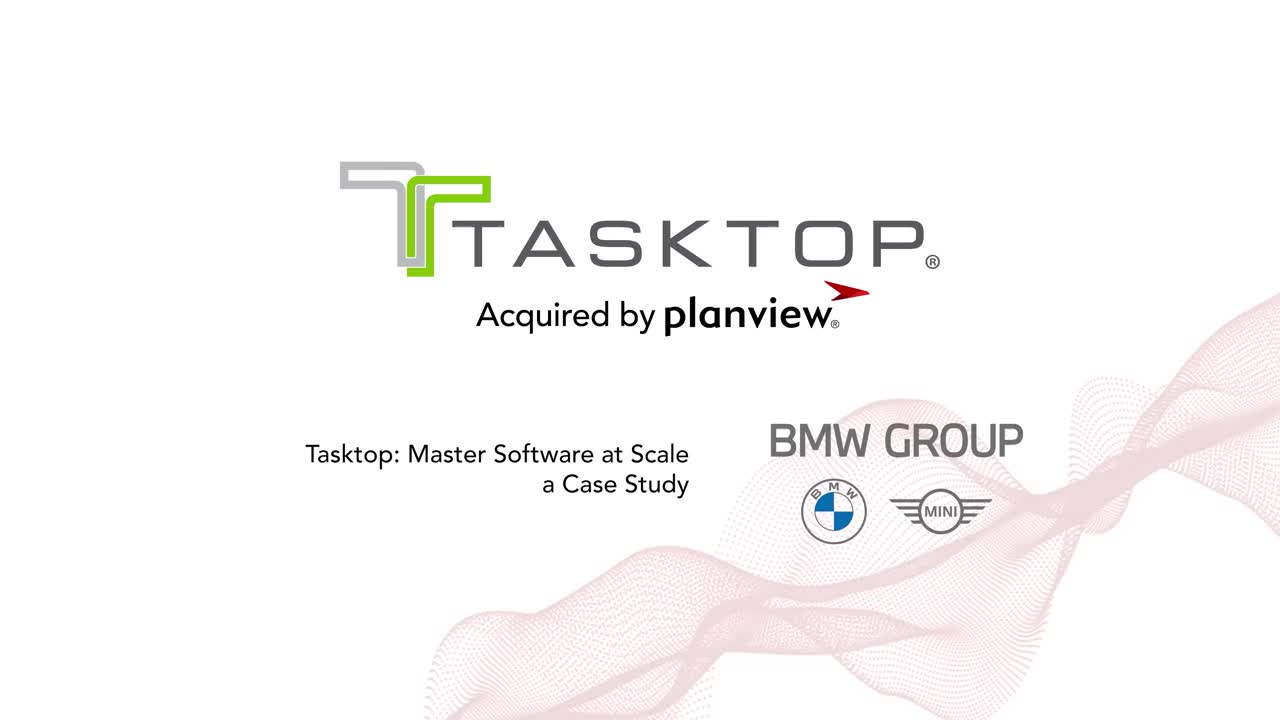
The Challenge
In recent years, corporate IT has changed drastically, forcing the entire BMW Group through an Agile transformation. Everything must be cloud-ready, scalable, networked, connected, and secure. International cooperation, distributed supply chains, and globally distributed teams are becoming increasingly important.
The Solution
BMW has been working closely with Planview® since 2011. Planview supports BMW by running the data supply from Germany to its R&D center in China, providing data integration for the testing and validation of the control unit development (E/E), as well as ensuring data consistency within its Agile toolchains. A key project was completed one year ahead of plan, despite challenges from the Covid-19 pandemic.
ABOUT THE BMW GROUP
The BMW Group is a German multinational manufacturer of performance luxury vehicles and motorcycles headquartered in Munich, Bavaria, Germany. With 31 production and assembly facilities in 15 countries as well as a global sales network, is the world’s leading manufacturer of premium automobiles and motorcycles, and provider of premium financial and mobility services.
Its Chinese joint venture, BMW Brilliance Automotive, aspires to be the leading sustainable provider of first-class individual mobility across the entire value chain of China’s automotive industry. Its business operations include R&D, procurement, production, sales, and after-sales services of BMW automobiles in China. The joint venture has around 23,000 employees and more than 430 local content suppliers. In 2021, BBA produced more than 700,000 BMW cars, making it the largest producer of premium cars in China.
CHALLENGE: CONNECTING TOOLS, DATA, AND PROCESSES
BMW has a simulation center at their Chinese joint venture, BMW Brilliance Automotive, in Shenyang, China. “If you want to grow as an international company, you must be in China. The fundamental challenge here is that if you want to sell cars in China, you have to develop them there."
BMW understood that in order to be successful in the demanding Chinese market, the processes and protocols used to attain BMW’s high standard of quality had to be replicated to achieve the desired results. The goal was to enable BBA’s vehicle simulation R&D center to operate in accordance with BMW’s German model. This included setting up the highperformance computing clusters, rolling out the relevant software, training the local employees, developing new software, and, most importantly, enabling data supply from Germany to run the simulations.
SOLUTION: AN INTEGRATED TOOLCHAIN ACROSS GEOGRAPHIES
BMW had been working with Planview since 2011 on challenges related to data integration, Agile working methods, and value stream management.
“The most important areas where Planview supports BMW are the simulation data supply in China, the data integration at E/E, data consistency in our Agile toolchains, and, more increasingly, questions about the Flow Framework®."
The BBA project has been a big success in which Planview played a big part.
“Planview helped me run the data supply chain from Germany to China and back – not only for IT relevant data, for example, from Jira to Jira, but also for engineering data that is required to run the simulations."
RESULTS: PROJECT COMPLETION ONE YEAR EARLY
With the help of Planview, BMW completed the whole project one year earlier than planned. “We reached the target business milestones exactly. The simulation work could be started on schedule, despite COVID.”
The organization can now integrate different software products with each other much faster than before. At the same time, the team is better able to gain new insights from their data and use it to become better and faster.
FUTURE: VISIBILITY INTO BOTTLENECKS
Looking into the future, the organization is starting to use Planview® Viz to reap even more benefit from their data and gain greater insights into their processes. “In my opinion, for an organization to be efficient, it’s imperative to think about where one’s own weaknesses and bottlenecks lie. If you don’t know this, you run the risk of focusing on the wrong things and falling behind the competition.”
“It is important to give the teams methods and tools to check themselves, measure themselves, and find out how each individual and the team as a whole can improve. You have to constantly ask yourself how you can get better, because if you stop getting better, you stop being good. And ultimately, we want to continue building the best cars in the world."
See what Planview solutions can do for your organization. View demos on demand at Planview.com/demos.
Looking to connect with like-minded business and technology professionals?
The Flow Framework Community provides a professional, inclusive, and supportive environment for learning, questioning, and networking on all topics related to the Flow Framework, Flow Metrics, and value stream management (VSM). flowframework.org/community
More Case Studies
-
Vanguard
Vanguard, a substantial player in the investment management landscape, embarked on a five-year modernization journey in 2020 to enhance its digital channels and improve investor outcomes.
View case study -
Viessmann
Viessmann’s Zero Waste Journey: How a Climate Solution Provider Modernized Their IT Toolchain to Eliminate Waste and Inefficiency
View case study