We’re building the future of connected work
with market-leading portfolio management and value stream management solutions
Planview enables organizations to connect the business from ideas to impact, accelerating the achievement of what matters most. Our full spectrum of portfolio management and value stream management solutions creates an organizational focus on the strategic outcomes and empowers teams to deliver their best work, no matter how they work. The comprehensive Planview platform and enterprise success model enables our customers to transform at the speed of opportunity and deliver competitive products, services, and customer experiences.
-
Improve time-to-value and predictability
Consistently meet customer and market commitments with early warnings into constraints. Planview enables more accurate planning – leveraging leading indicators and better capacity assumptions – and shortens the time from ideas to business outcomes. -
Increase efficiency to unlock capacity
Keep your teams focused on strategic objectives by using embedded goal tracking throughout the flow of work. Planview provides deep visibility into capacity utilization, helping business leaders reduce operational costs and redeploy resources by proactively identifying and addressing waste and constraints. -
De-risk your strategic bets
Confidently tackle uncertainty when internal or external conditions change. Planview delivers complete, actionable data that empowers business leaders to compare and prioritize strategic initiatives – based on risk and tradeoff scenarios – to maximize business outcomes.
Planview Platform for Connected Work
Drive successful transformation and pivot with speed
See how the Planview Platform for Connected Work connects the strategic direction and goals of business leaders to the bottom-up innovation and delivery of teams – accelerating time to value, increasing efficiency to unlock capacity, increasing predictability, and de-risking strategic investments.
Watch Platform Demo • Watch Platform DemoFive reasons to make Planview your transformation partner
-
Planview helps connect strategy, teams, and outcomes
We help you translate strategy into business results for your most important initiatives and keep your organization and processes aligned. Only Planview delivers the tightest connection between the strategy and priorities at the top and the decisions and work at the team level.
-
Planview makes dynamic planning and prioritization a reality
We know you have to plan with incomplete information and uncertainties. Only Planview helps you plan, replan, and instantly see the potential impact under different scenarios.
-
Planview delivers powerful connectivity across your enterprise applications and tools
Optimize productivity and scale faster without sacrificing cross-functional collaboration with seamlessly connected tools, from planning to delivery. Planview is the only partner that brings your enterprise applications and software development lifecycle tools together to give you a holistic view of your technology landscape.
-
Planview is built for your growth and transformation journey
We understand all the ways you work and how you are trying to transform. Planview enables all types and combinations of work, methodologies, and practices.
-
Planview is a trusted and proven partner
Our support for your success does not end with our software. Planview’s market and thought leadership, along with our proven success methodology and playbooks, ensure that we will guide you throughout your journey.
Learn more
- Nationwide Building Society
- Citi
- Dell
- Novartis
- Agropur
- Allianz
- DaVita
- Viessmann
- VW Volkswagen
- Box
- NatWest
- Walmart
- Diageo
- Pfizer
- AkzoNobel
- UPS United Parcel Service
- Beam
- Conagra Brands
- Volvo
- Danone
- Siemens
- Roche
- De Beers Jewelers
- Honeywell
- MetLife
- EA Sports
- BCBS Blue Cross Blue Shield
- Vodafone Group
- Commonwealth Bank
- Abbott Nutrition
- Thermo Fisher Scientific
- ABB Group
- Johnson & Johnson
Planview is a recognized innovator and industry leader
Planview has been recognized time and time again for our contributions to Portfolio and Work Management innovation, making us a unique partner for accelerating transformation. See what industry analysts have to say.
-
- Named a Leader in the 2023 Gartner® Magic Quadrant™ for Adaptive Project Management and Reporting
- Named a Leader in the 2023 Gartner® Magic Quadrant™ for Strategic Portfolio Management
- Named a Leader in the 2022 Gartner® Magic Quadrant™ for Enterprise Agile Planning Tools
-
- Named a Leader in The Forrester Wave™, Value Stream Management, Q4 2022
- Named a Leader in The Forrester Wave™, Strategic Portfolio Management Tools, Q1 2022
-
- Named a Leader in IDC MarketScape: Worldwide Strategic Portfolio Management and IT Project and Portfolio Management 2023–2024 Vendor Assessment — Driving Adaptive Business Optimization with AI and Connected Data
- Named a Leader in the IDC MarketScape: Worldwide Value Stream Management and Agile Project and Portfolio Management 2023-2024 Vendor Assessment – Leveraging AI for Dynamic, Agile Value Creation
-
- Named a Leader in the 2023 GigaOm Radar for Value Stream Management
- Named a Leader and a Fast Mover in the 2022 GigaOm Radar for Value Stream Management
-
- Named a Technology Leader in Quadrant SPARK Matrix™: Strategic Portfolio Management Q3 2023
- Named a Technology Leader in Quadrant SPARK Matrix™: Project and Portfolio Management Q3 2023
- Named a Technology Leader in the Quadrant SPARK Matrix™: Value Stream Management (VSM), 2023
- Named a Technology Leader in the Quadrant SPARK Matrix™: Enterprise Agile Planning, 2023
- Named a Technology Leader in the Quadrant SPARK Matrix™: Innovation Management, 2023
Gartner does not endorse any vendor, product or service depicted in its research publications and does not advise technology users to select only those vendors with the highest ratings or other designation. Gartner research publications consist of the opinions of Gartner’s Research & Advisory organization and should not be construed as statements of fact. Gartner disclaims all warranties, expressed or implied, with respect to this research, including any warranties of merchantability or fitness for a particular purpose.
GARTNER is a registered trademark and service mark of Gartner, Inc. and/or its affiliates in the U.S. and internationally, and MAGIC QUADRANT is a registered trademark of Gartner, Inc. and/or its affiliates and are used herein with permission. All rights reserved.
NatWest
“While transformation is largely dependent on culture and behavior, it also requires the right people, process, and tools. Planview enables NatWest [formerly RBS] to maintain a controlled environment and provide transparency of delivery across our Agile teams. At the same time, we are able to track the main-level financial data, outcomes, and business cases, and ultimately the delivery of value throughout our business domains (value streams). You don’t go from one end of the Agile journey in one go. It’s a transition, step by step, and Planview is helping us get there.”
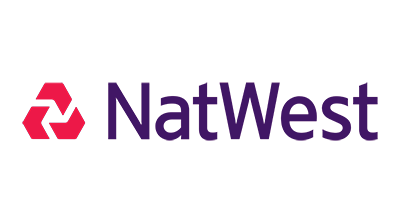
Flowserve Corporation
“Our goal is pretty simple: be adaptive and flexible to change. As a result, we are constantly evolving our product portfolio and business models in our many locations. This allows us to be more progressive about how teams work together and prioritize work based on location. With Planview, our strategic partnership means we have a close day-to-day working relationship that extends far beyond a simple piece of software. We love how quickly we can apply new models of working to our business processes, organization roles and responsibilities, and to our metrics.”
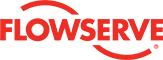
Eric van Gemeren
Chief Transformation Officer, Flowserve Corporation
MIK + ONE PODCAST
Moving from Project to Product
Join Mik Kersten, Planview CTO and author of Project to Product as he sits down with software delivery leaders and innovators and delves into how they deliver value and drive digital transformations in their organizations.
Browse Podcasts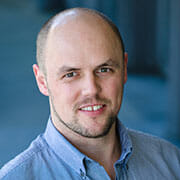
Dr. Mik Kersten
Chief Technology Officer, Planview
-
Featured eBook
The Insider’s Guide to Modern PPM
What other guides won’t tell you about how to evolve portfolio management approaches and the technology to get there
Get the eBook • The Insider’s Guide to Modern PPM -
Adaptive Portfolio Planning: 5 Steps to Achieve Greater Agility for Your Transformation Journey
Become a strategic execution leader that drives value while adapting to disruption
Get the eBook • Adaptive Portfolio Planning: 5 Steps to Achieve Greater Agility for Your Transformation Journey -
Deliver Digital Transformation at Speed
These seven recommendations will help you achieve the results your clients, investors and board are demanding
Get the eBook • Deliver Digital Transformation at Speed
Insight from subject matter experts
Are you ready to explore how Planview can help your organization drive on-strategy delivery at speed?
Planview has one mission: to build the future of connected work, from ideas to impact. Planview helps organizations accelerate the achievement of what matters most, supporting our customers from need to speed, from passion to progress, and from overhead to optimization. Our connected platform of solutions underpins the business and digital transformations of more than 4,500 customers globally, including 59 of the Fortune 100. Planview empowers enterprises to improve time-to-market and predictability, increase efficiency to unlock capacity, and ensure their most strategic initiatives deliver the desired business outcomes.
