Table of contents
The term Kanban system refers to using Kanban boards and cards to manage work, improve workflow, and practice continuous improvement. Kanban systems harness the power of visual management to help teams maximize time and efficiency.
Kanban 101: Supercharge your team’s productivity
By encouraging teams to identify, prioritize, and intentionally complete work items one at a time, Kanban can help combat the damaging effects of multitasking in a hyper-stimulated world.
View the eBook • Kanban 101AgilePlace Free Trial: AgilePlace Online Kanban Software
Sign up for a 30-day free trial and you and your team can start building online Kanban boards today. Experience for yourself how AgilePlace supports continuous delivery initiatives, eliminates waste and improves your team’s delivery processes and speed.
Start your Free Trial • AgilePlace Free Trial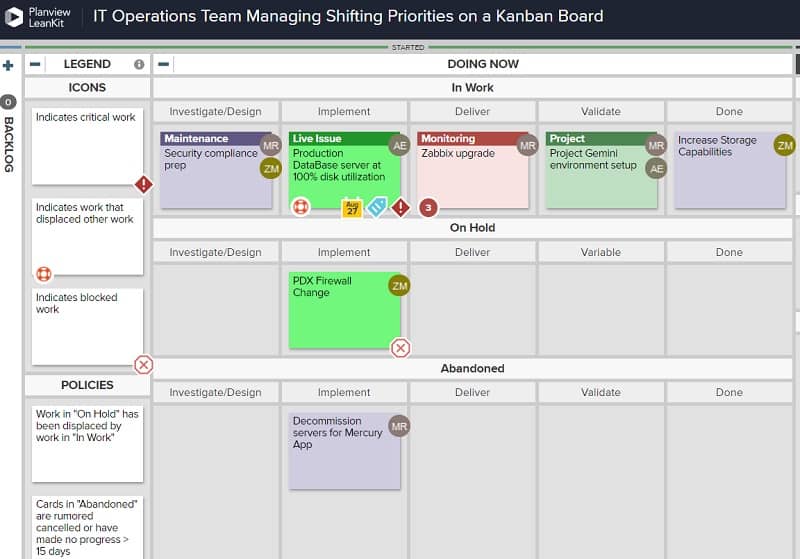
Here’s why you should consider implementing a Kanban system with your team.
Why Use a Kanban System?
When it comes to identifying opportunities for improvement like using a Kanban system, your busy team members are among the people who can provide the most insight.
However, pulling these people off task and facilitating their input may not seem possible. After all, who will get the work done while the team is brainstorming and implementing improvements?
This is the unfortunate catch-22 that many teams find themselves in: Because they’re too busy to make improvements, things that could alleviate some of their busyness don’t get finished. So, the cycle of inefficiency continues.
To overcome the challenges of having too much work and not enough time to take a step back, many teams have found a Kanban system to be a good starting point.
A Kanban system offers a systematic approach to identifying opportunities for improving efficiency by tracking and managing work in a visual way.
Kanban isn’t a separate improvement-focused initiative that pulls people away from their “actual” work. It’s a systematic approach to tracking and managing a team’s work that, when used correctly, will naturally highlight opportunities for improvement. When teams identify those opportunities, they can implement solutions and track their progress on the same Kanban board.
With a Kanban system, “doing the work” and “improving the way we work” can be performed simultaneously – helping teams truly embrace the continuous part of continuous improvement.
The Roots of the Kanban System: The Kanban Ordering System
You might be surprised to learn that Kanban didn’t always involve virtual boards and cards. Kanban originated on the shop floors of Japanese automotive manufacturer Toyota.
Toyota engineers were looking for ways to reduce waste and increase the efficiency of their manufacturing processes. They looked to an unlikely source of inspiration: The local grocery store.
Grocery stores use visual cues to guide their inventory management — they order more products only when inventory drops below a certain threshold. The stores used physical cards to indicate when levels were low.
Imagine a row of a certain type of crackers on a grocery store shelf. A card would be placed a few boxes from the end of the row, signaling that it was time to order more of those crackers.
Toyota engineers took this concept of ordering materials “just in time,” and developed what became known as Kanban, or the Kanban ordering system.
A card would be attached to completed products. When those products (in this case, vehicles) were sold, the cards would be taken to the front of the line, signaling to produce more products.
Cards were also attached to the raw materials being used for production; when materials were used, their cards would be sent to the front of the line, signaling for more materials to be ordered.
Using this Kanban system helped Toyota drastically reduce waste by streamlining their inventory management. Just-in-time (JIT) manufacturing, and other Kanban principles and practices that came from it, spread throughout automotive manufacturing and into other industries.
A Kanban System for Software Development and Beyond
The Kanban system we know today, which involves the use of virtual boards and cards to track work as it moves through a process, largely took shape in the later part of the last century, when it was embraced by software development teams.
TUnlike the manufacture of physical goods, the development of software isn’t something that is tangible; raw materials are not manipulated on an assembly line to create physical objects. Instead, the work of software development happens within the minds of developers – it’s one of many types of knowledge work.
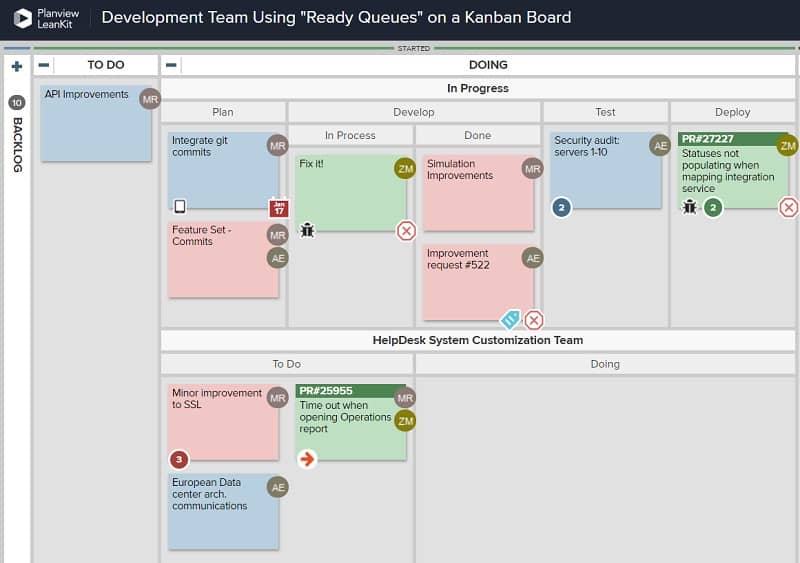
Software development was a new type of work that required a different type of workflow. Teams needed a way to:
- Practice iterative development
- Balance multiple types of work
- Align efforts across the team
They needed to be able to track, measure, and improve upon their processes in the same place.
The Kanban system, as we know it today, emerged as a highly flexible, visual tool that enabled software development teams to manage their work in a way that made sense for their workflows.
Since then, Kanban has been used by virtually every type of team in every industry.
What is a Kanban System?
A Kanban system is a workflow management structure that encourages visibility, transparency, and accountability across teams. Using a Kanban system can help teams get a clearer sense of:
- The specific steps in their process
- How work flows (or stumbles) through that process
- How workloads are balanced (or not) across the team
- Where waste exists in the process
- Where opportunities to streamline processes might exist
- How work items are related or connected
- Performance metrics, such as lead time, cycle time, and more
For most teams, the increased visibility, transparency, and accountability enable greater levels of productivity and efficiency than they ever thought possible.
Elements of a Kanban System
You might be familiar with Kanban boards and cards: But what exactly do we mean by a Kanban system?
The phrase refers to how Kanban boards and cards are used by a team or organization to visualize and manage their work. A Kanban system includes:
- Using Kanban boards to reflect existing workflows
- Using Kanban cards to represent work items
A single team using a single board to manage its work can make up a Kanban system. But part of the power of Kanban lies in its scalability; many organizations scale Kanban across teams and departments, creating hierarchies of connected boards and cards. This is also a Kanban system.
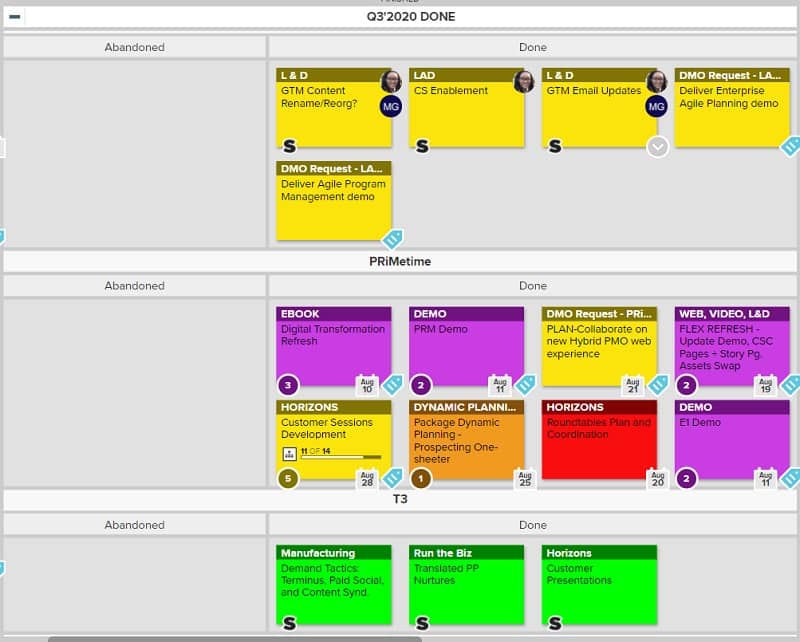
In summary, when Kanban boards and cards are used to manage work by any group of individuals, it is a Kanban system.
Benefits of a Kanban System
A good Kanban system goes a long way in helping teams understand how their time is being spent. Most online Kanban tools provide tracking and productivity data that helps people easily identify problem areas.
Once they have a better idea of where the problems lie, teams can begin to develop solutions to those problems. Maybe one team member is severely overworked, while another doesn’t have enough work to fill his or her day. In this instance, a manager would help to delegate tasks to team members who have more bandwidth, alleviating the pressure from the overworked individual and removing the impediment for the entire team.
Another way in which a Kanban system helps to maximize resources lies in the ability to efficiently deliver products while continuously improving the process required to get there. Software development teams, accounting teams, finance teams and even creative agencies have adopted the use of the Kanban system, despite its lack of emphasis on due dates.
By delivering products continuously, customers gain the benefits of using those products sooner and the ability to make modifications based on new information that has become available since the start of the last project phase.
Because the principles of Kanban may not exactly fit the needs of all organizations, some Lean / Agile teams use a combination of methods along with other methodologies, including Agile Scrum and Extreme Programming (XP), as they seek to deliver products that meet the business requirements and exceed expectations of the time it takes to deliver work.
While some Scrum and XP teams follow more specific processes that entail their own set of project management techniques, all team members can benefit from using a Kanban board to visually communicate information that is otherwise difficult to process, understand or retain.
Not only is visual data easier to understand, it allows for a certain amount of creativity and innovation necessary for so much of the knowledge work being done today.
Advantages of Using the Kanban System
There are many advantages to using the Kanban system as a way to manage work, including:
- Flexibility
- Focus on continuous delivery
- Reduction of wasted work / wasted time
- Increased productivity
- Increased efficiency
- Team members’ ability to focus
First, Kanban is flexible. There are no prescribed phase durations, and priorities are constantly reassessed based on the most recent information.
Another advantage to using Kanban is the focus on continuous delivery. By delivering small portions of a project continuously to the customer, teams have multiple opportunities to synchronize future iterations with the updated business requirements. In this way, teams can ensure they are delivering exactly what the customer wants.
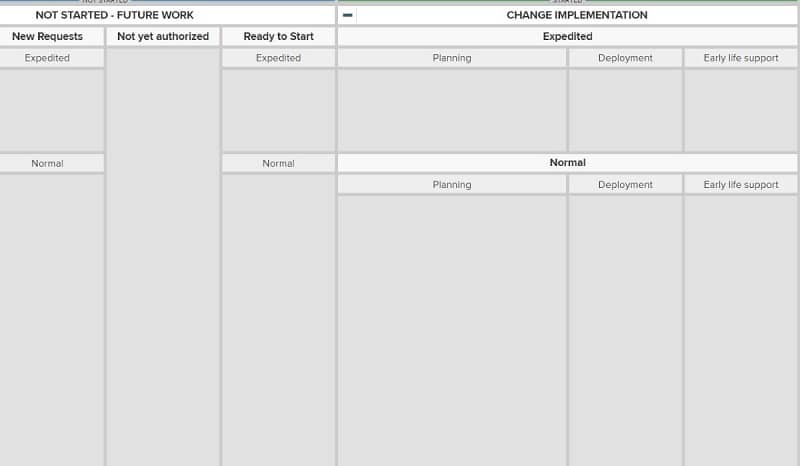
Other advantages to using Kanban revolve around productivity and efficiency, two concepts that also tie back to the reduction of waste. A well-designed Kanban system helps teams to identify and reduce process waste in all of its forms.
You can think of process waste as anything that does not add value to the customer. It can come in the form of:
- Work that is not needed (excess inventory)
- Work that does not meet success criteria
- Duplicated effort
- Overprocessing
- Idle time
- Unnecessary motion
- Administrative overhead that does not add value to the process
- Time spent doing the wrong work (work that has less value), rather than focusing on the work with more value
When waste is eliminated from a process, project or workflow, productivity goes up, people are able to focus more on the work that matters, and efficiency is improved in the way people manage their time and in the way they do their work.
Finally, when work is properly re-prioritized as needed and communicated visually using a Kanban system or task board, an individual doesn’t have to question what to work on next. Instead, the team member pulls the next Kanban card from the top of the queue without spending any time considering which task to pull next.
Let’s explore the concept of “pulling” tasks in more detail.
The Kanban Pull System
Using Kanban helps teams switch from “push” to “pull” systems. A push system is what happens naturally in teams: One person completes their part of a piece of work, and then “pushes” it to the next person without regard for their capacity. You might have heard this referred to as “throwing (a piece of work) over a wall.”
The problem with operating in a push system is that it doesn’t encourage teams to actually operate as a system. Instead, individuals operate in functional silos – performing their functions as opposed to collaborating cross-functionally, leading to miscommunications, frustration, and resentment. It’s especially easy to operate in a push system when work is not visualized, because issues like bottlenecks aren’t easily recognized.
When teams visualize their work in a Kanban system, they can begin to see the entire team’s work as a system.
They can see where work piles up, where it gets stuck, and where the system is overwhelmed. They are armed with the visibility and insight to begin to practice a pull system – where work items are pulled into the queue by the people doing the work as they complete tasks, in order of priority.
Instead of person A pushing work over a wall to person B, person A and person B work together to decide when to start that work. When the system has capacity for that project to begin, person A performs their part, then when they are ready, person B pulls it onto their plate.
Using Kanban to implement a pull system helps to increase accountability, transparency, and collaboration across teams – leading to better collaboration, less waste, and more predictable delivery.
Get Started with a Kanban System
We recommend that all teams implementing a Kanban system practice the exercises in the Kanban Roadmap. These exercises are designed to help teams define their existing processes and map them on a Kanban board. From there, teams can identify and implement opportunities for improvement.
It’s also helpful to learn as much as you can about how to customize your Kanban boards and cards. Looking at Kanban examples from teams similar to yours can serve as helpful inspiration as well.
The most important thing to remember is that your Kanban system should be an accurate reflection of your true process, because you must understand where you are to see how to get where you want.